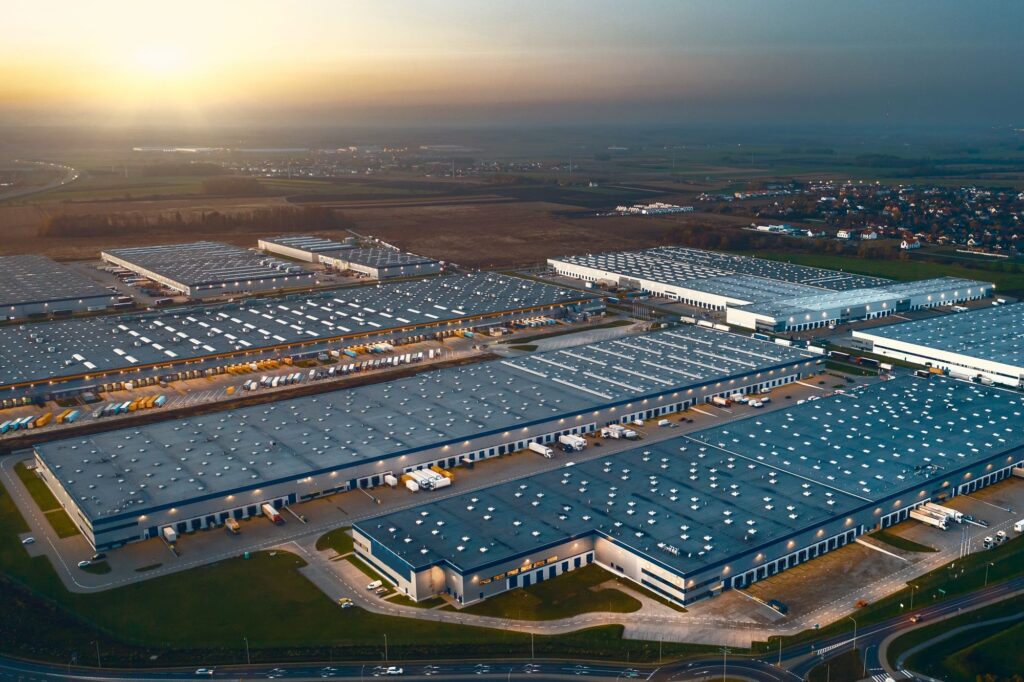
Device management: Enhancing logistics efficiency through innovative solutions
Identification and reporting of energy consumption per customer to meet requirements set by the European Union and own sustainability initiatives.
- Identification of all energy consumers
- Division of costs per customer parcel
- Increase efficiency by effortless device management
- Integration of remote Application Updates
Together, we’ll evaluate your requirements and discuss how to implement energy management digitization using our analysis tools.
Asset management and data analytics – anytime, anywhere
Creating a sustainable and efficient logistics
A global logistics real estate leader, that focuses on developing, leasing, and managing efficient and sustainable logistics and distribution centers supports clients in optimizing their supply chains. Well-known customers utilize specific plots within the company’s locations to enhance their delivery capabilities, allowing for quicker customer fulfillment.
Identify and record needs
The aim was to ensure that the energy data generated by vehicles, lighting and warehouse robots for individual parcels could be passed on to customers based on the recorded energy data. Due to its global component of the project, the need for a remote device management and application update was given.
Providing value beyond the hardware
In the first step, all installed hardware devices receive the Application Update simultaneously. Additionally, changes to applications can now be made from anywhere, providing flexibility and convenience.
Here the Application Update cuts update time by up to 70%, saving over 150 working hours across 250 devices.
Technical hardware setup in the logistics center
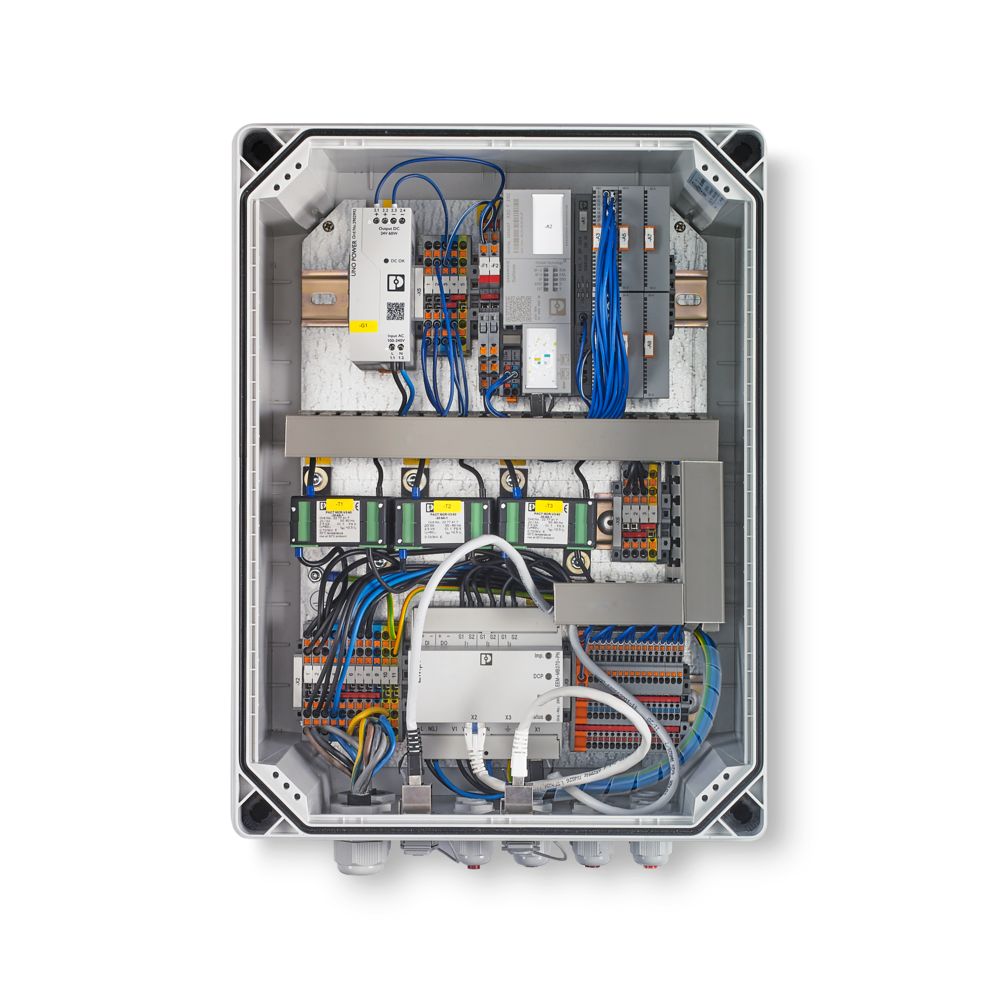
Technical Implementation with Phoenix Contact hardware
The project was implemented by using a Data Collection Box for signal recording and measurements, alongside a PLCnext Control with IIoT framework. Configuration occurred through web-based management. The Secure Edge Box facilitated data forwarding to higher-level and established cloud systems. The project involved engineering services, PLCnext Technology, TC Router, EMpro energy measuring devices, connectivity products and power supplies by Phoenix Contact. The PLCnext controller with EMpros energy meters recorded energy consumption, sending data to the cloud.
Over 250 devices were registered. PLCnext Technology enabled centralized data collection from energy meters to cloud interfaces. TC Routers sent data to various cloud instances, providing secure remote access for maintenance. Phoenix Contact Engineering Services offer pre- and post-commissioning support, including acceptance testing and technical services.
Maximize value with Smart Services
The Smart Services of Proficloud.io added the needed digitalization component of the project.
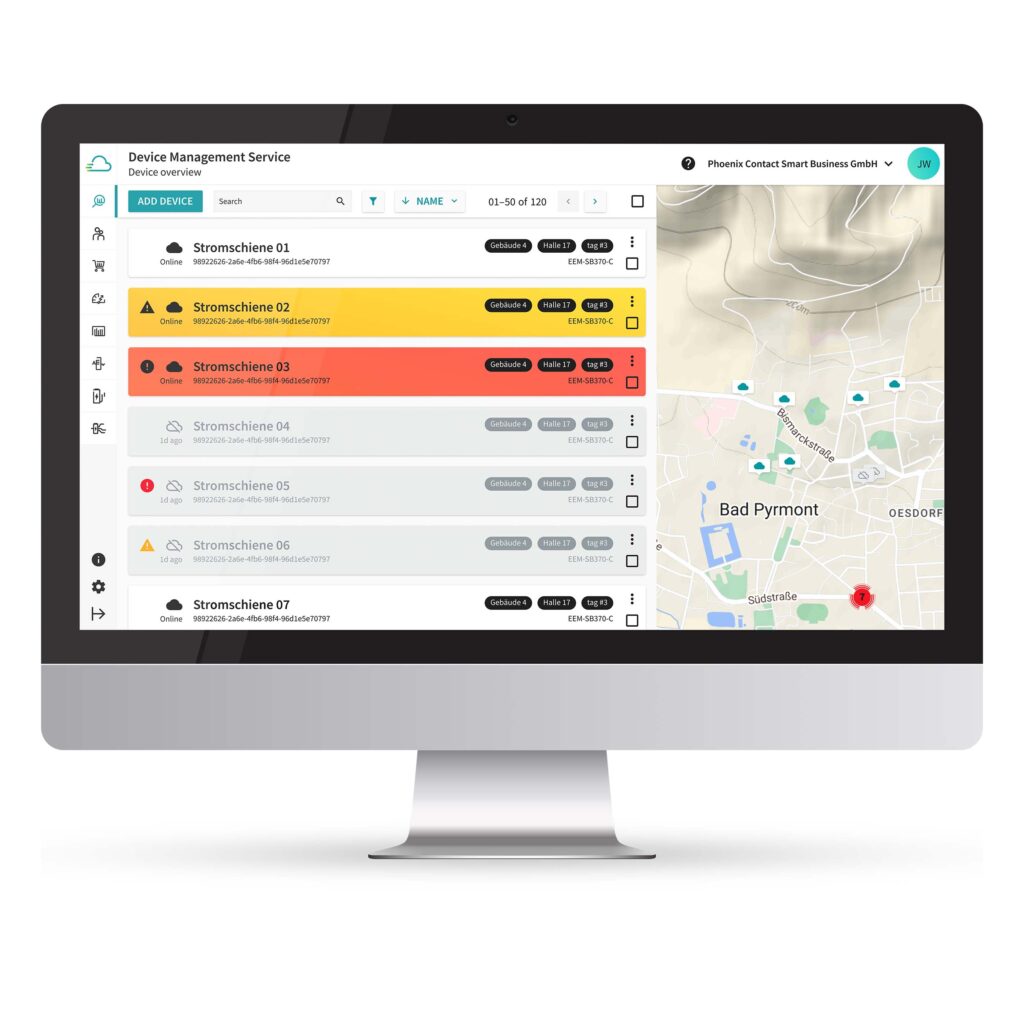
Managing high volumes of devices simultaneously
With its ability to manage high number of devices simultaneously, Proficloud.io streamlined device management through the Smart Services, Device Management Service and the Device Management Service Basic Add-on, saving time and enhancing flexibility. It replaced the time-consuming individual changes made for each hardware device.
Further, the Device Management Service offers standardized, application-independent device information in real time on Proficloud.io for Phoenix Contact and third party devices.
The DMS Basic Add-on is the first add-on for the Device Management Service and offers the possibility to create groups of individual devices, a notification system for the health status of your devices and an Application Update (currently PLCnext hardware) remotely.
View into the Dashboard of the project
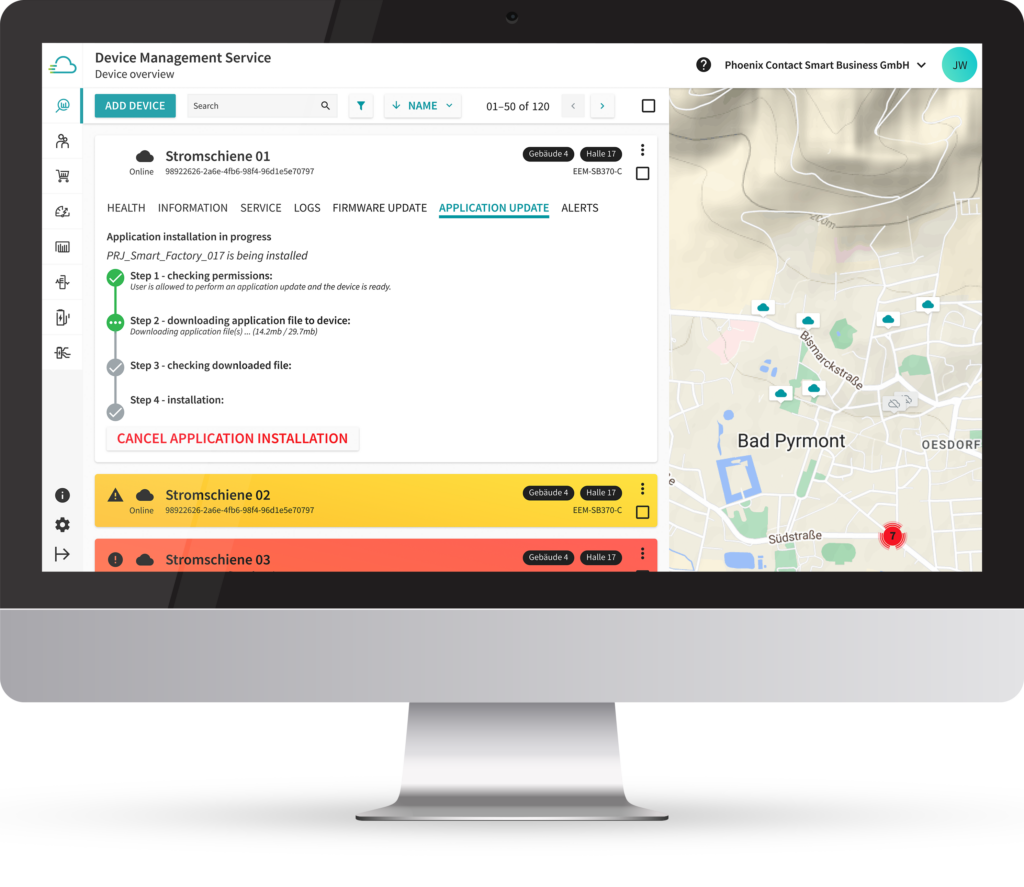
Saving up to 70 % of time for Application Updates
In this project, the time for an update was reduced by up to 70% through the Application Update via Proficloud.io – with more than 250 devices, this means over 150 working hours are saved.
Applications (in the Phoenix Contact cosmos) are exports from PLCnext Engineer that can be installed and executed on PLCnext devices. Normally, the controllers (e.g. AXC F 2152) must be connected directly to a PC or via VPM to a PC. With the Application Update in the DMS Basic Add-on, these applications can also be transferred remotely. A direct connection to the PC or via VPN is therefore no longer necessary.
Overcoming challenges
Collaborative efforts improve application update process
Working closely together with all parties, the team was able to work out how the Application Update works best. One thing to consider was the PLCnext Engineer version with which the project file was created. There were several attempts to find a solution and during a productive meeting with everyone involved in the process a solution on how to create the right version was found.
The platform Proficloud.io was initially unable to interpret the file correctly and partially aborted the update process. During the process the update process was solidified and made more stable. The Application Update of the Device Management Service has become more reliable as a result.
In addition, the platform now saves the timestamp of an individual step, which increases transparency and makes debugging easier.
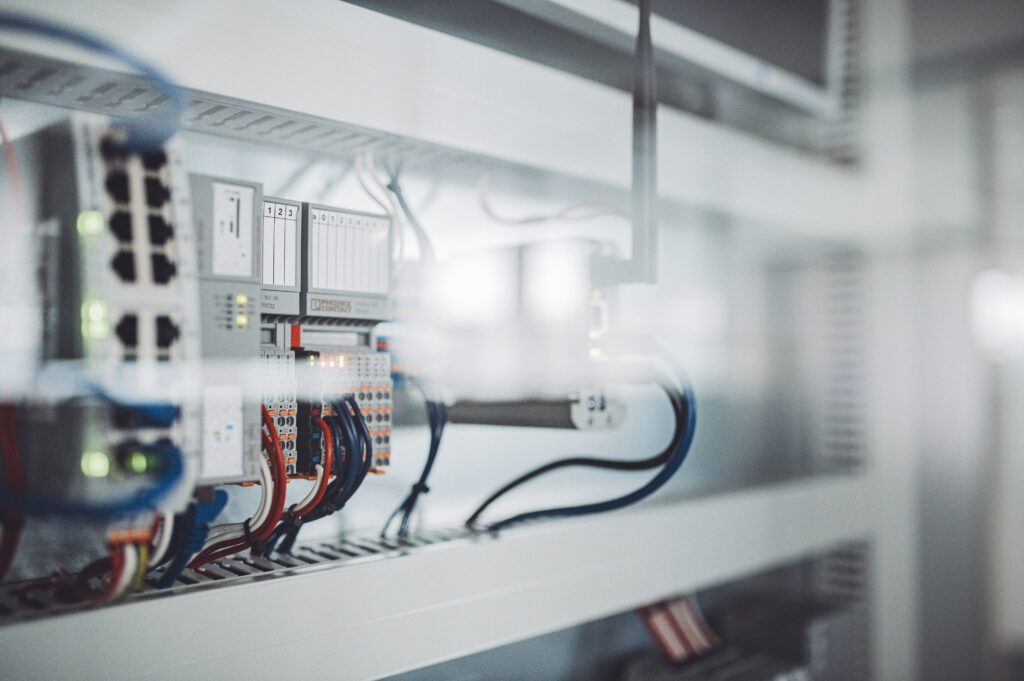
Further information
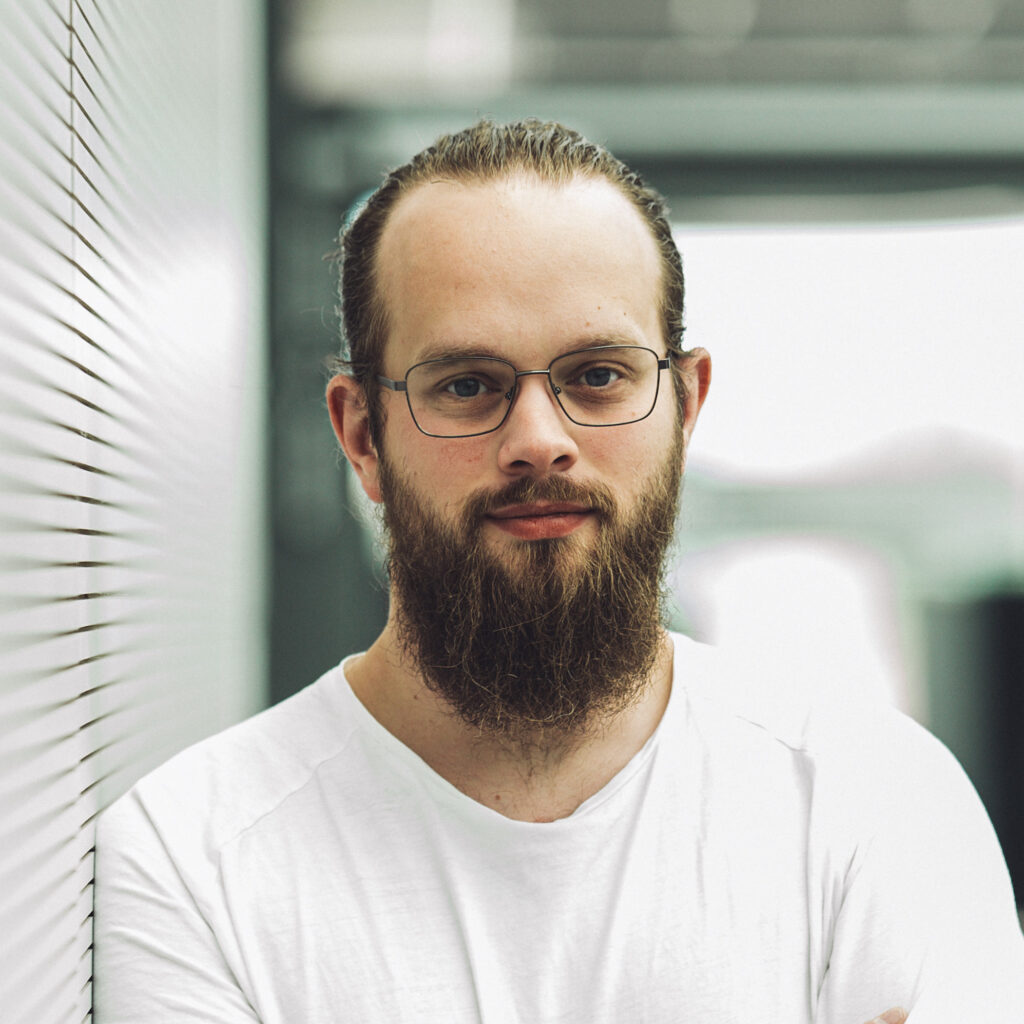
Hi, my name is Florian Jacob and I am glad to help you out!
Please do not hesitate to contact me. Also, if you have any suggestions or comments, just send us a message to inbox[at]phoenixcontact-sb.io and we will answer as soon as possible.